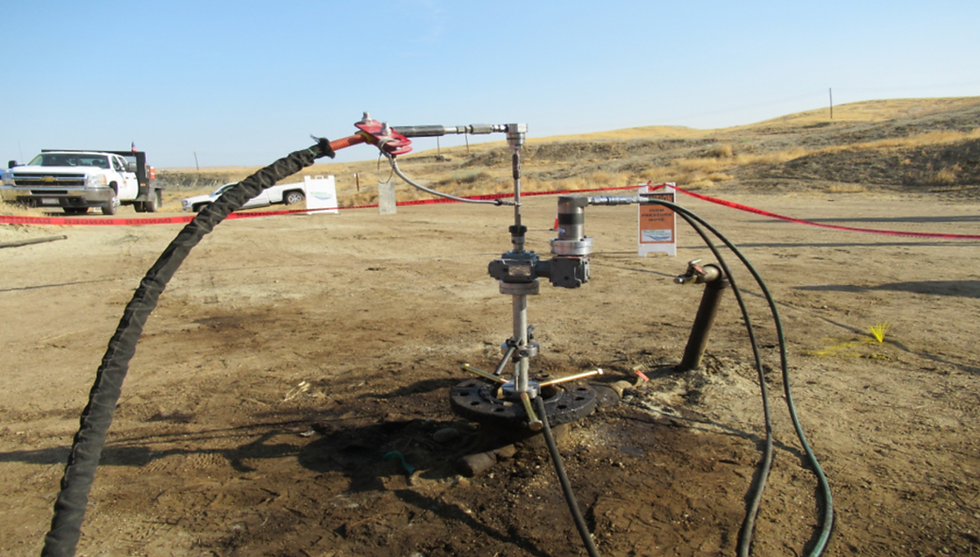
Case Study Overview
When compared to conventional excavation cut-and-cap processes, NuWave's downhole, high-pressured waterjet methodology provides a dramatic cost savings to our clients.
Traditionally, a cut-and-cap process would involve a large footprint to be dug out, exposing the surrounding area of the wellhead. In this particular Case Study from a job site in California, NuWave offered a clear advantage to the client by providing a solution that did not require lost production on the surrounding wells.
There is no flame when cutting with NuWave's internal subsurface radial-track cutting waterjets. This means that production can continue while surrounding wells are being cut-and-capped.
When there is no flame, there is no loss of production. There is no hot work permits required. Our methodology for cut-and-cap is more efficient and is the new standard of best practice.
Komentar